A coupling sleeve is a cylindrical part with internal threads, primarily used to connect the shank adapter and drill rod, as well as to connect drill rods. By aligning the internal threads of the coupling sleeve with the external threads of the drill rods or shank adapter, a secure and tight connection is formed, ensuring the stability and reliability of rock drilling operations.
Types of Coupling Sleeves
Coupling sleeves are available in two structural types: full-bridge coupling sleeves and reducing coupling sleeves. The coupling sleeves provided by our company are mainly used for drifting drilling and deep-hole drilling.
Types | Introduction | Application | Thread |
Full-Bridge Coupling Sleeve | Features better disassembly and a tighter connection; less chance of getting stuck. | It is commonly used in outdoor construction projects. | R32、R38、T38、T45、T51 |
Reducing Coupling Sleeve | This sleeve has a bridging section in the middle without threads. The coupling sleeve has ended with different thread specifications, designed for connecting products with varying thread sizes. | It is suitable for high-torque drilling machines. |
More Parameters
Coupling sleeve type: full bridge coupling sleeve and reducing coupling sleeve
Thread size: R32, R38, T38, T45, T51.
Coupling Sleeves | Length | Diameter | Thread | Weight | ||
mm | inch | mm | inch | (kg) | ||
![]() |
155 | 6 1/8 | 44 | 1 3/4 | R32 | 1 |
150 | 5 7/8 | 35 | 1 3/8 | R25 | 0.7 | |
160 | 6 5/16 | 38 | 1 1/2 | R25 | 1.3 | |
150 | 5 7/8 | 45 | 1 3/4 | R25-R32 | 1.1 | |
160 | 6 5/16 | 45 | 1 3/4 | R25-R32 | 1.2 | |
160 | 6 5/16 | 56 | 1 13/64 | R25-R38 | 2.5 | |
170 | 6 3/4 | 56 | 1 13/64 | R25-T38 | 3.2 |
Coupling | Length | Diameter | Thread | Weight | ||
mm | foot | mm | inch | (kg) | ||
![]() |
150 | 5 7/8 | 44 | 1 3/4 | R32 | 1 |
150 | 5 7/8 | 50 | 1 37/64 | R28 | 0.9 | |
170 | 6 3/4 | 55 | 2 5/32 | R38 | 2 | |
160 | 6 5/16 | 45 | 1 3/4 | R28-R32 | 1.2 | |
160 | 6 5/16 | 56 | 1 13/64 | R28-R38 | 2.5 |
Coupling | Length | Diameter | Thread | Weight (kg) |
||
mm | inch | mm | inch | |||
![]() |
170 | 6 3/4 | 55 | 2 5/32 | R38 | 1.8 |
190 | 7 1/2 | 55 | 2 5/32 | T38 | 2.0 | |
150 | 6 1/8 | 45 | 1 3/4 | R25-R32 | 1.1 | |
160 | 6 1/4 | 45 | 1 3/4 | R25-R32 | 1.2 | |
160 | 6 1/4 | 45 | 1 3/4 | R28-R32 | 1.2 | |
160 | 6 1/4 | 55 | 2 5/32 | R32-R38 | 1.8 | |
170 | 6 3/4 | 55 | 2 5/32 | R32-R38 | 2.0 | |
180 | 7 1/16 | 55 | 2 5/32 | R32-R38 | 2.2 | |
210 | 8 1/4 | 55 | 2 5/32 | R32-R38 | 2.8 | |
170 | 6 3/4 | 56 | 2 1/8 | R32-T38 | 2.1 | |
180 | 7 1/16 | 56 | 2 1/8 | R32-T38 | 2.2 | |
210 | 8 1/4 | 56 | 2 1/8 | R32-T38 | 2.8 | |
190 | 7 1/2 | 63 | 2 33/64 | R32-T45 | 3.2 |
Coupling | Length | Diameter | Thread | Weight (kg) | ||
mm | inch | mm | inch | |||
![]() |
150 | 6 1/8 | 44 | 1 3/4 | R3212 | 1.0 |
160 | 6 1/4 | 44 | 1 3/4 | R3212 | 1.1 | |
160 | 6 1/4 | 48 | 1 7/8 | R3212 | 1.5 |
Coupling | Length | Diameter | Thread | Weight (kg) | ||
mm | foot | mm | inch | |||
![]() |
150 | 6 1/8 | 44 | 1 3/4 | R32 | 1.0 |
160 | 6 1/4 | 44 | 1 3/4 | R32 | 1.1 |
Coupling | Length | Diameter | Thread | Weight (kg) | ||
mm | inch | mm | inch | |||
![]() |
170 | 6 3/4 | 55 | 2 5/32 | HL38 | 1.9 |
190 | 7 1/2 | 55 | 2 5/32 | HL38 | 2.1 |
Coupling | Length | Diameter | Thread | Weight (kg) | ||
mm | inch | mm | inch | |||
![]() |
190 | 7 1/2 | 55 | 2 5/32 | T38 | 2.1 |
Coupling | Length | Diameter | Thread | Weight (kg) | ||
mm | inch | mm | inch | |||
![]() |
210 | 8 1/4 | 63 | 2 33/64 | T45 | 3.0 |
210 | 8 1/4 | 66 | 2 37/64 | T45 | 3.3 |
Coupling | Length | Diameter | Thread | Weight (kg) | ||
mm | inch | mm | inch | |||
![]() |
225 | 8 7/8 | 71 | 2 51/64 | T51 | 4.6 |
225 | 8 7/8 | 76 | 3 | T51 | 4.8 | |
235 | 9 1/4 | 72 | 2 7/8 | T51 | 4.7 | |
235 | 9 1/4 | 77 | 3 1/32 | T51 | 4.9 |
Can't find the parameters you want? Please get in touch with us!
Download BrochureAdvantages
High-Quality Steel Materials
Our coupling sleeves are made from high-quality steel that offers excellent mechanical and physical properties, as well as a dense crystal structure. This results in high density, strength, toughness, outstanding wear resistance, and corrosion resistance.
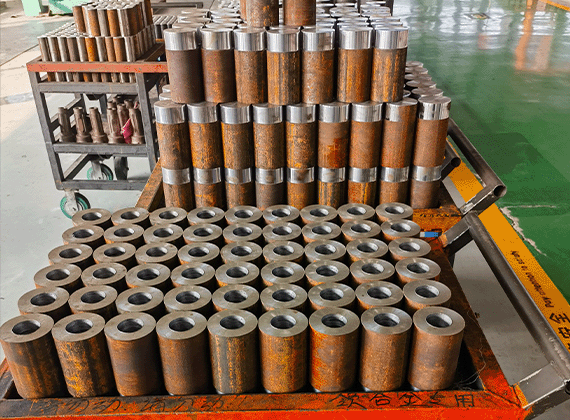
Advanced Manufacturing Processes
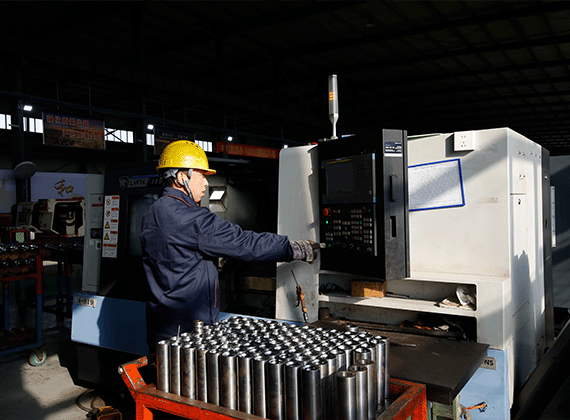
We use advanced manufacturing techniques to ensure our products have high precision and superior performance. Using CNC machinery and other precise equipment for processing, as well as optimizing the structural design of the coupling sleeve, we ensure tight compatibility between the coupling sleeve and the drill rods, enhancing the strength and wear resistance of the connection.
Strict Quality Control
We implement strict quality control throughout the production process of coupling sleeves. From raw material inspection to monitoring the production process and through to finished product inspection and testing, we take stringent measures to ensure that the product quality meets relevant standards and customer requirements.
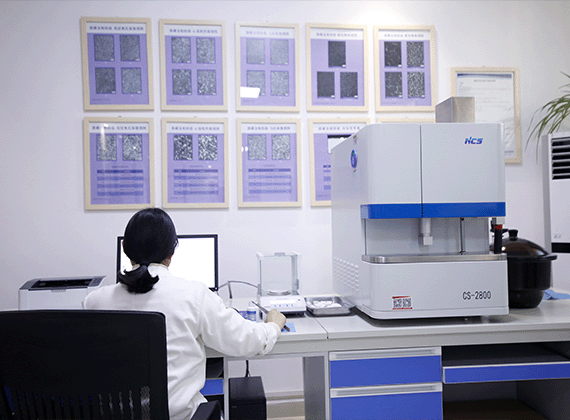