Drill rods are tools used to connect the rock drill bits to drilling equipment for rock or soil excavation. These tools are often utilized in mining, tunneling, and hydraulic engineering projects.
Types of Drill Rods
We offer lightweight and heavy-duty drill rods. Lightweight rods include Tapered Drill Rods, Shank Rods, and Integral Drill Rods. Heavy-duty rods are mainly used in excavation drill jumbos for underground mining, tunneling, and open-pit operations.
Lightweight Drill Rods
Types | Brief Introduction | Application | Length |
Tapered Drill Rod ![]() |
The rod is a hexagonal hollow shaft with a shank structure that connects to drilling equipment. The head of the rod is tapered to connect with tapered bits. | This rod is suitable for drilling softer rock formations such as shale and mudstone. | 600mm-8000mm Without shank, regular shank is 108 mm |
Shank Rod ![]() |
The rod is a hexagonal hollow shaft with a shank structure that connects to drilling equipment. The head of the rod has a threaded shape, allowing it to connect with threaded bits. | This rod is designed for small-diameter drilling tasks and is suitable for medium to hard rock layers. | 610mm-3600mm Without shank, regular shank is 108 mm |
Integral Drill Rod ![]() |
The shank, shoulder, drill rod, and rock drill bit are combined as a single integrated drill rod. | This is suitable for shallow hole drilling in softer rock layers such as fractured rock and weathered rock. | 800mm-8000mm Without shank, regular shank is 108 mm |
Heavy-Duty Drill Rods
Types | Brief Introduction | Application | Length |
Extension Rod ![]() |
This rod has external threads on both ends. | It is widely used in step drilling, anchor bolt drilling, oil extraction drilling, long-hole drilling, and small-hole drilling. | 915mm-6095mm |
MF Rod ![]() |
This rod has male threads on one end and female threads on the other. | It is ideal for long-hole and high-precision drilling, ensuring minimal deviation. | 610mm-6400mm |
Drifter Rod | This rod is mainly used with fully hydraulic rock drills. | It is suitable for underground mining tunnel blasting, anchor hole drilling, and excavation for traffic tunnels, hydropower project water diversion tunnels, and other underground construction projects. | 2100mm-6100mm |
Guide Rod | The primary function is to accurately direct the drill bit to the intended drilling location. | It is mainly utilized for open terrace drilling and underground long-hole drilling. | 1220mm-6095mm |
More Parameters
Drill rods are divided into R thread and T thread, models include R25, R28, R32, R38, T38, T45, T51, etc. Different product types and models can be selected according to different engineering requirements.
11° Tapered Drill Rod
Drill Rod | Shank | Length | Weight (kg) |
||||||
mm | foot | ||||||||
Hex Tapered Rod |
H22×108mm | 610 | 2' | 2.20 | |||||
1220 | 4' | 4.10 | |||||||
1830 | 6' | 5.90 | |||||||
2000 | 6'7" | 6.40 | |||||||
2435 | 8' | 7.80 | |||||||
2600 | 8'8" | 8.30 | |||||||
3200 | 10'6" | 10.10 | |||||||
3655 | 12' | 11.50 | |||||||
4000 | 13'1" | 12.60 | |||||||
4800 | 15'9" | 14.90 | |||||||
5600 | 18'4" | 17.40 | |||||||
6400 | 21' | 19.80 | |||||||
7200 | 23'6" | 22.20 | |||||||
8000 | 26'2" | 24.60 |
12° Tapered Drill Rod
Drill Rod | Shank | Length | Weight (kg) | ||||||
mm | foot | ||||||||
Hex Tapered Rod |
H22×108mm | 610 | 2' | 2.20 | |||||
1220 | 4' | 4.10 | |||||||
1830 | 6' | 5.90 | |||||||
2000 | 6'7" | 6.40 | |||||||
2435 | 8' | 7.80 | |||||||
2600 | 8'8" | 8.30 | |||||||
3200 | 10'6" | 10.10 | |||||||
3655 | 12' | 11.50 | |||||||
4000 | 13'1" | 12.60 | |||||||
4800 | 15'9" | 14.90 | |||||||
5600 | 18'4" | 17.40 | |||||||
6400 | 21' | 19.80 | |||||||
7200 | 23'6" | 22.20 | |||||||
8000 | 26'2" | 24.60 | |||||||
H25×159mm | 1830 | 6' | 7.96 | ||||||
2435 | 8' | 10.38 | |||||||
3050 | 10' | 12.84 | |||||||
3655 | 12' | 15.26 | |||||||
3965 | 13' | 16.50 | |||||||
4270 | 14' | 17.72 | |||||||
4880 | 16' | 20.16 | |||||||
5530 | 18' | 22.76 | |||||||
6095 | 20' | 25.02 |
R32
Drill rod | Length | Diameter | Thread | Weight (kg) |
|||||
mm | foot | mm | inch | ||||||
Drifter Rod |
2400 | 7'10" | 32 | 1 1/4 | T38-R32 | 15.3 | |||
3090 | 10'11/2" | 32 | 1 1/4 | T38-R32 | 19.8 | ||||
3400 | 11'13/4" | 32 | 1 1/4 | T38-R32 | 21.7 | ||||
4000 | 13'13/8" | 32 | 1 1/4 | T38-R32 | 25.5 | ||||
4310 | 14'11/2" | 32 | 1 1/4 | T38-R32 | 27.5 | ||||
4920 | 16'11/2" | 32 | 1 1/4 | T38-R32 | 31.3 | ||||
5530 | 18'11/2" | 32 | 1 1/4 | T38-R32 | 35.2 | ||||
3090 | 10'11/2" | 35 | 1 3/8 | T38-R32 | 24.0 | ||||
3700 | 12'11/2" | 35 | 1 3/8 | T38-R32 | 28.7 | ||||
4000 | 13'13/8" | 35 | 1 3/8 | T38-R32 | 31.1 | ||||
4310 | 14'11/2" | 35 | 1 3/8 | T38-R32 | 33.4 | ||||
4920 | 16'11/2" | 35 | 1 3/8 | T38-R32 | 37.8 | ||||
5530 | 18'11/2" | 35 | 1 3/8 | T38-R32 | 42.9 | ||||
6100 | 20' | 35 | 1 3/8 | T38-R32 | 47.3 | ||||
MF Rod |
3700 | 12'11/2" | 35 | 1 3/8 | T38-R32 | 29.0 | |||
4310 | 14'11/2" | 35 | 1 3/8 | T38-R32 | 34.1 | ||||
4920 | 16'11/2" | 35 | 1 3/8 | T38-R32 | 38.8 | ||||
5530 | 18'11/2" | 35 | 1 3/8 | T38-R32 | 43.6 | ||||
6400 | 21' | 35 | 1 3/8 | T38-R32 | 50.3 |
T38
Drill Rod | Length | Diameter | Thread |
Weight (kg) |
|||||
mm | foot | mm | inch | ||||||
Extension Rod |
1220 | 4' | 39 | 1 1/2 | T38-T38 | 10.2 | |||
1525 | 5' | 39 | 1 1/2 | T38-T38 | 12.8 | ||||
1830 | 6' | 39 | 1 1/2 | T38-T38 | 15.3 | ||||
2435 | 8' | 39 | 1 1/2 | T38-T38 | 20.4 | ||||
3050 | 10' | 39 | 1 1/2 | T38-T38 | 25.5 | ||||
3660 | 12' | 39 | 1 1/2 | T38-T38 | 30.9 | ||||
3965 | 13' | 39 | 1 1/2 | T38-T38 | 33.2 | ||||
4270 | 14' | 39 | 1 1/2 | T38-T38 | 35.7 | ||||
4880 | 16' | 39 | 1 1/2 | T38-T38 | 41.0 | ||||
5530 | 18'11/2" | 39 | 1 1/2 | T38-T38 | 46.3 | ||||
6095 | 20' | 39 | 1 1/2 | T38-T38 | 50.9 | ||||
MF Rod |
915 | 3' | 39 | 1 1/2 | T38-T38 | 10.7 | |||
1220 | 4' | 39 | 1 1/2 | T38-T38 | 13.3 | ||||
1525 | 5' | 39 | 1 1/2 | T38-T38 | 15.8 | ||||
1830 | 6' | 39 | 1 1/2 | T38-T38 | 18.3 | ||||
3050 | 10' | 39 | 1 1/2 | T38-T38 | 28.5 | ||||
3660 | 12' | 39 | 1 1/2 | T38-T38 | 33.6 | ||||
4270 | 14' | 39 | 1 1/2 | T38-T38 | 38.7 | ||||
4880 | 16' | 39 | 1 1/2 | T38-T38 | 43.7 | ||||
5530 | 18'11/2" | 39 | 1 1/2 | T38-T38 | 49.2 | ||||
6095 | 20' | 39 | 1 1/2 | T38-T38 | 53.9 | ||||
Hex Extension Rod |
1220 | 4' | 32 | 1 1/4 | T38-T38 | 8.6 | |||
1830 | 6' | 32 | 1 1/4 | T38-T38 | 12.6 | ||||
2435 | 8' | 32 | 1 1/4 | T38-T38 | 16.6 | ||||
3050 | 10' | 32 | 1 1/4 | T38-T38 | 20.8 | ||||
3660 | 12' | 32 | 1 1/4 | T38-T38 | 24.9 | ||||
DoubIe Thread Rod |
3050 | 10' | 46 | 1 3/4 | T38-T38 | 25.7 | |||
3660 | 12' | 46 | 1 3/4 | T38-T38 | 30.9 | ||||
Guide Speed Rod |
1830 | 6' | 46 | 1 3/4 | T38-T38 | 23.5 | |||
3050 | 10' | 46 | 1 3/4 | T38-T38 | 37.2 | ||||
3660 | 12' | 46 | 1 3/4 | T38-T38 | 44.0 | ||||
4270 | 14' | 46 | 1 3/4 | T38-T38 | 50.9 | ||||
4880 | 16' | 46 | 1 3/4 | T38-T38 | 57.7 | ||||
5530 | 18'11/2" | 46 | 1 3/4 | T38-T38 | 65.0 | ||||
6095 | 20' | 46 | 1 3/4 | T38-T38 | 71.3 | ||||
1220 | 4' | 56 | 2 1/8 | T38-T38 | 12.6 | ||||
1525 | 5' | 56 | 2 1/8 | T38-T38 | 14 | ||||
1830 | 6' | 56 | 2 1/8 | T38-T38 | 17.4 | ||||
3050 | 10' | 56 | 2 1/8 | T38-T38 | 28.3 | ||||
3660 | 12' | 56 | 2 1/8 | T38-T38 | 32.8 | ||||
4920 | 16'2" | 56 | 2 1/8 | T38-T38 | 47.9 | ||||
3660 | 12' | 64 | 2 1/2 | T38-T38 | 51 |
ST58
Drill Rod | Length | Diameter | Thread | Weight (kg) |
|||||
mm | foot | mm | inch | ||||||
![]() |
1525 | 5' | 76 | 2 3/8 | ST58-ST58 | 34.0 | |||
1830 | 6' | 76 | 2 3/8 | ST58-ST58 | 40.0 | ||||
3660 | 12' | 76 | 2 3/8 | ST58-ST58 | 76.3 |
ST68
Drill Rod | Length | Diameter | Thread | Weight (kg) |
|||||
mm | Foot | mm | inch | ||||||
![]() |
1525 | 5' | 87 | 3 7/16 | ST68-ST68 | 35.5 | |||
1830 | 6' | 87 | 3 7/16 | ST68-ST68 | 43.8 | ||||
3660 | 12' | 87 | 3 7/16 | ST68-ST68 | 80.0 | ||||
6110 | 20' | 87 | 3 7/16 | ST68-ST68 | 133.0 |
Can't find the parameters you want? Please get in touch with us!
Download BrochureAdvantages
High-Quality Steel Material Selection
Lightweight Drill Rods
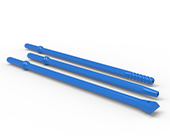
· Our rods are primarily made from 40SiMnCrNiMo, a high-strength and high-toughness alloy steel known for its excellent wear resistance and fatigue resistance. Additionally, we offer customized services using 23CrNi3Mo material to meet customers' demands for increased strength and enhanced wear resistance.
· 40SiMnCrNiMo and 23CrNi3Mo materials have high yield and tensile strengths, which can withstand great shocks and vibrations in harsh operating environments, ensuring the drill rods' long-term stability and durability.
Heavy-Duty Drill Rods
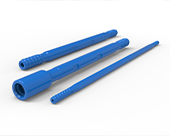
· Our heavy-duty drill rods are produced using 23CrNi3Mo, a high-performance alloy structural steel known for its exceptional strength, toughness, and good hardenability.
· These 23CrNi3Mo heavy-duty drill rods can endure greater impact and torque, making them ideal for more complex working environments and heavier tasks. It ensures both work efficiency and safety.
Advanced Manufacturing Process
· Precision Forging : We use advanced precision forging technology, carefully controlling the temperature, pressure, and deformation during the forging process to ensure uniform material properties and a dense structure, improving the mechanical performance and fatigue resistance of the rods.
· Heat Treatment Optimization : After forging, we perform strict heat treatment processes, including quenching and tempering, to eliminate forging stresses, increase hardness and toughness, and ensure excellent wear and impact resistance during operation.
· Precision Machining : After heat treatment, we use advanced CNC machining equipment for precision processing, including turning, milling, and grinding, to ensure the rods meet the required dimensional accuracy and surface quality.
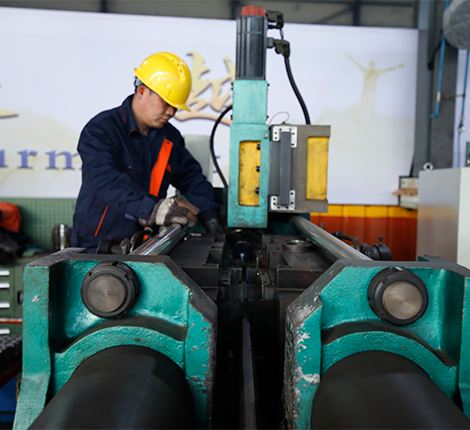
Strict Quality Control
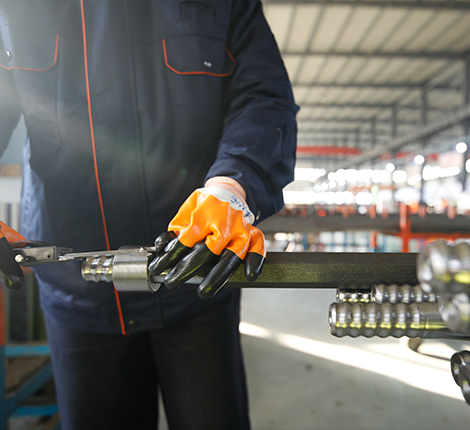
· Raw Material Inspection : We perform strict inspections on each batch of steel during the procurement stage, including chemical composition analysis and mechanical performance testing, to ensure the raw materials meet design specifications.
· Process Control: Throughout the manufacturing process, we monitor and control every step, including real-time monitoring of forging temperature, pressure, and deformation, as well as temperature and time control during heat treatment, ensuring process stability and control.
· Final Product Inspection: In the finished product stage, each drill rod undergoes strict inspections, including appearance checks, dimensional measurements, and mechanical performance tests, to ensure the rods meet design specifications and customer requirements.
Drill Rod
Production Process
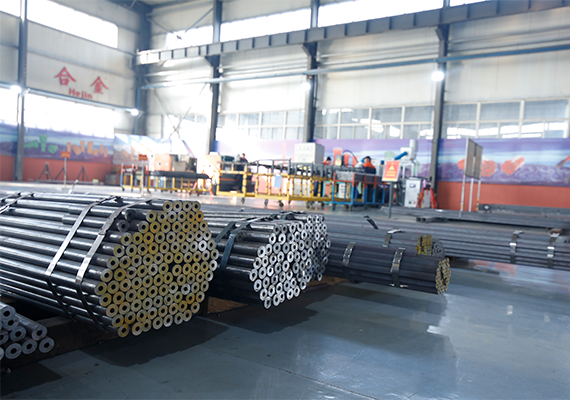
Raw Material Preparation and Inspection
· Material Selection
according to the use and performance requirements of drill rods, choose suitable steel as raw material, such as hexagonal hollow steel, hollow round steel, etc.
· Material Inspection
Purchased raw materials undergo strict inspections, including chemical composition analysis and mechanical testing, ensuring the materials meet design specifications.
Cutting and Processing
· Length Cutting
The raw material is precisely cut according to the design length, resulting in the required drill rod blanks.
· Threading Both Ends
The ends of the drill rod blanks are threaded using machining equipment for connection to other components. For certain types, like MF rods, friction welding processes are employed to create female threads.
· Machining Handling Grooves
Grooves are machined on the drill rods for easy handling and installation.
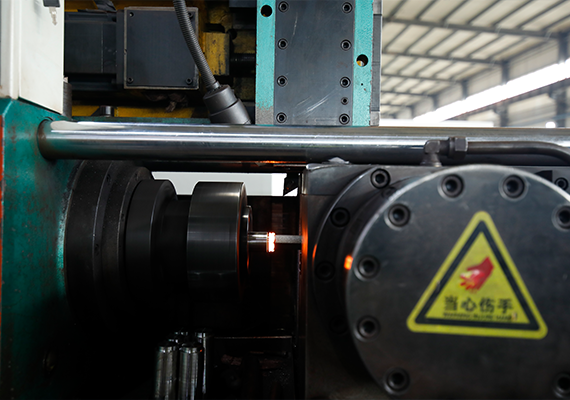
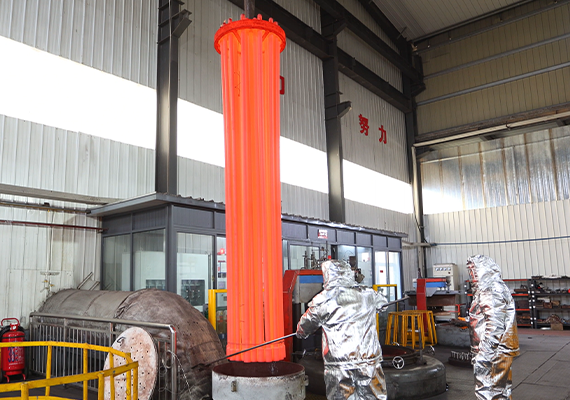
Heat Treatment
· Carburizing
The drill rod is placed in a deep-well carburizing furnace for carburizing to increase its carbon content and surface hardness.
· Quenching
After carburizing, the drill rod is placed in a wind-cooling quenching tower to increase hardness and wear resistance.
· Tempering
After quenching, the drill rod undergoes tempering in a deep-well tempering furnace to eliminate quenching stresses and enhance toughness and stability.
Straightening and Surface Treatment
· Straightening
The heat-treated drill rods are straightened to ensure that their shape and dimensions meet the design requirements.
· Shot Peening
The surface of the drill rod is shot peened by shot peening equipment to remove the surface oxidized layer and increase the surface strength to improve the friction with other parts.
· Phosphating
The drill rod surface is phosphate to enhance corrosion resistance.
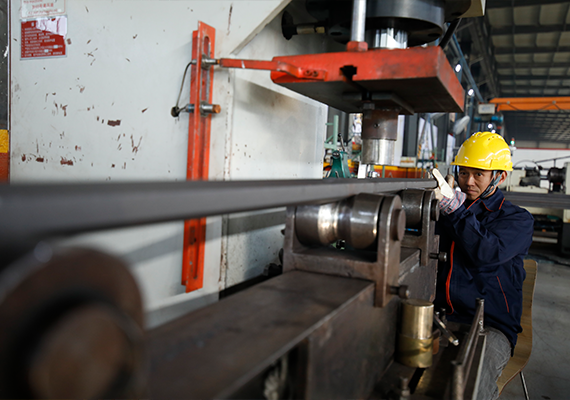
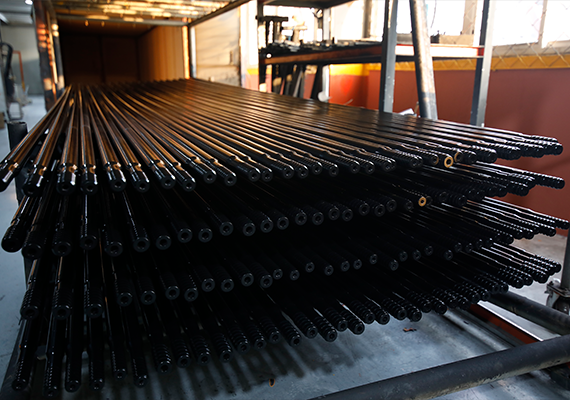
Inner Hole Cleaning and Anti-Corrosion Treatment
· Carburizing
use professional equipment to clean the bore of the drill rod to ensure that the bore is unobstructed.
· Surface Coating
Anti-corrosion paint is applied to the surface of the drill rod to improve its corrosion resistance and extend its service life.
Plastic Sleeve Installation and Labeling
· Plastic Sleeve
A plastic sleeve is added to the threaded areas of the drill rod to protect the threads from damage and ease disassembly.
· Production Labeling
A production label is applied to each drill rod, containing information such as production date, batch number, and specifications for traceability and management.
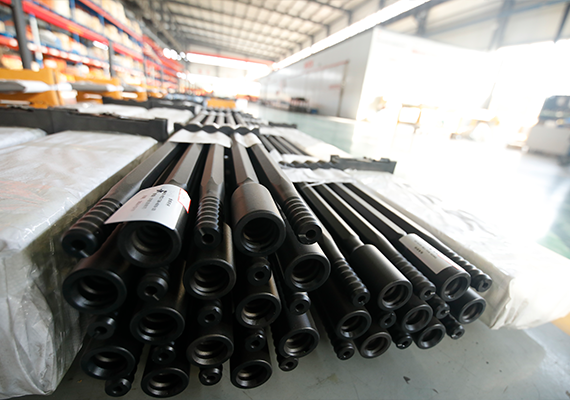
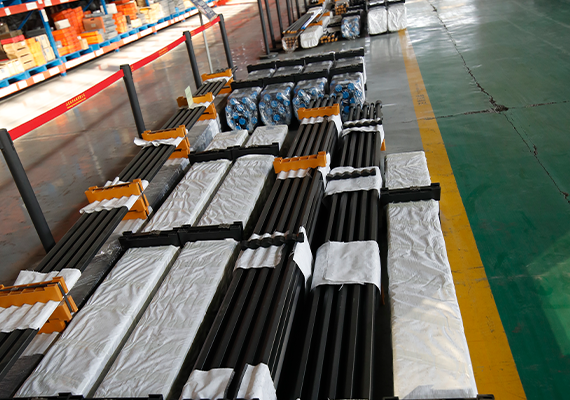
Storage and Final Inspection
·Storage
Finished drill rods are stored in the warehouse and stored for shipment.
· Final Inspection
Before storage, each drill rod undergoes a final inspection to ensure it meets design specifications and customer requirements.