A Down-the-Hole (DTH) hammer is a rock-drilling tool powered by compressed air. It operates by driving an internal piston reciprocally to deliver powerful impacts to the drill bit, effectively breaking rock. It is widely used in metallurgy, coal, chemical industry, building materials, and other mining industries, as well as water conservancy, hydropower, highway, railroad, national defense, construction, and other basic energy construction fields.
Types of DTH Hammers
DTH hammers can be classified based on different specifications:
Type |
Description |
According to working pressure |
low air pressure DTH hammer (working pressure at 0.5-0.7Mpa), medium air pressure DTH hammer (0.7-1.2Mpa) and high air pressure DTH hammer (Above 1.2Mpa) |
According to gas distribution method and structural characteristics |
Valved and unvalved DTH Hammers |
Formed by center through-hole |
Ordinary and Reverse Circulation DTH Hammers |
More Parameters
Outer Diameter (mm) | Length (mm) | Drilling Diameter (mm) | Working Pressure (MPa) | Air Consumption (m³/min) | Connection with Drill Pipe | Connection with Drill Bit | Weight (kg) | Specifications |
φ61.2 | 745 | φ65-φ70 | 0.5-0.7 | 2.5 | M42X10X1.5P | φ37-4 | 13 | KQC65 |
φ67.2 | 803 | φ72-φ74 | 0.5-0.7 | 3 | M48X10X2P | φ43-6 | 14 | KQC70 |
φ67.2 | 766 | φ74-φ76 | 0.5-0.7 | 3 | M48X10X2P | φ44-4 | 15 | KQC76 |
φ72 | 796 | φ80-φ82 | 0.5-0.7 | 5 | API 2 3/8 Reg P | φ50-6 | 17 | KQC80 |
φ80.2 | 796 | φ90-φ130 | 0.5-0.7 | 5.5 | M48X10X2P | φ54-6 | 20 | KQC90A |
φ98 | 838 | φ110-φ150 | 0.5-0.7 | 11 | API 2 3/8 Reg B | φ65-6 | 30 | KQC110A |
φ137 | 908 | φ150-φ220 | 0.5-0.7 | 17 | M76X10X3B | φ90-6 | 75 | KQC150 |
φ156 | 1023 | φ175-φ250 | 0.5-0.7 | 19.5 | M100X28X10P | φ98-6 | 90 | KQC170 |
Outer Diameter (mm) | Length (mm) | Drilling Diameter (mm) | Working Pressure (MPa) | Air Consumption (m³/min) | Connection with Drill Pipe | Connection with Drill Bit | Weight (kg) | Specifications |
φ80.5 | 870 | φ90-φ120 | 0.8-1.2 | 6 | API 2 3/8 Reg P | φ54-6 | 25 | KQCZ90 |
φ98 | 917 | φ110-φ150 | 0.8-1.2 | 11 | API 2 3/8 Reg B | φ65-6 | 36 | KQCZ110 |
φ71 | 867 | φ80-85 | 0.8-2.1 | 3-12 | DZ50B | φ47-6 | 19 | KQCG80 |
φ81 | 908 | φ90-φ100 | 0.8-2.1 | 4.3-14.2 | API 2 3/8 Reg P | φ53-8 | 21.8 | KQCG90 |
φ92 | 1052 | φ105-φ130 | 0.8-2.1 | 3.5-18 | API 2 3/8 Reg B | φ64-8 | 38 | KQCG105 |
φ98 | 1034 | φ110-φ130 | 0.8-2.1 | 3.5-15 | API 2 3/8 Reg P | φ64-8 | 39 | KQCG110 |
φ98 | 994 | φ110-φ130 | 1.0-2.1 | 3.5-15 | API 2 3/8 Reg P | φ64-8 | 40 | KQCG110A |
φ98 | 998 | φ115-φ130 | 0.8-2.1 | 3-12 | API 2 3/8 Reg P | φ67-12 | 40 | KQCG115 |
φ114 | 1387 | φ130-φ152 | 0.8-2.1 | 5.7-18 | API 3 1/2 Reg P | φ84-8 | 69 | KQCG130 |
φ118 | 1067 | φ130-φ152 | 0.8-2.1 | 3-14 | API 2 3/8 Reg P | φ83-12 | 60 | KQCG130A |
φ124 | 1098 | φ140-φ152 | 1.0-2.1 | 4.5-18 | API 3 1/2 Reg P | φ84-8 | 74 | KQCG140 |
φ124 | 1220 | φ140-φ152 | 0.8-2.1 | 46.5-18 | API 3 1/2 Reg P | φ84-8 | 74 | KQCG140A |
φ136 | 1450 | φ152-φ305 | 1.0-2.1 | 8.5-25 | API 3 1/2 Reg P | φ99.5-8 | 126 | KQCG150 |
φ152 | 1372 | φ165-φ305 | 1.0-2.1 | 9-26 | API 3 1/2 Reg P | φ99.5-8 | 92 | KQCG165 |
φ146 | 1076 | φ165-φ203 | 0.8-2.1 | 6.8-20 | API 3 1/2 Reg P | φ104.4-12 | 92 | KQCG165A |
φ181 | 1551 | φ203-φ350 | 1.0-2.1 | 12-31 | API 4 1/2 Reg P | φ128-10 | 208 | KQCG200 |
φ186 | 1551 | φ203-φ350 | 1.0-2.1 | 12-35 | API 4 1/2 Reg P | φ128-10 | 228 | KQCG200A |
φ181 | 1450 | φ203-φ254 | 0.8-2.1 | 9.6-25 | API 4 1/2 Reg P | φ128-12 | 260 | KQCG200B |
φ181 | 1551 | φ203-φ350 | 1.0-2.1 | 12-31 | API 4 1/2 Reg P | φ128-10 | 228 | KQCG200C |
φ275 | 2110 | φ311-φ508 | 1.0-2.4 | 30-78 | API 7 5/8 Reg P | φ210-12 | 670 | KQCG310 |
Can't find the parameters you want? Please get in touch with us!
Download BrochureAdvantages
Our DTH hammers are designed to optimize drilling efficiency, delivering superior penetration rates and helping you reduce overall drilling costs.
High Efficiency
By integrating advanced impact and rotary technology, our DTH hammers significantly enhance drilling performance. Their optimized internal structure and efficient energy conversion mechanism ensure that every impact maximizes rock penetration, reducing downtime. Whether drilling through hard rock formations or tackling complex geological conditions, our hammers accelerate drilling speeds, saving valuable time for your project.
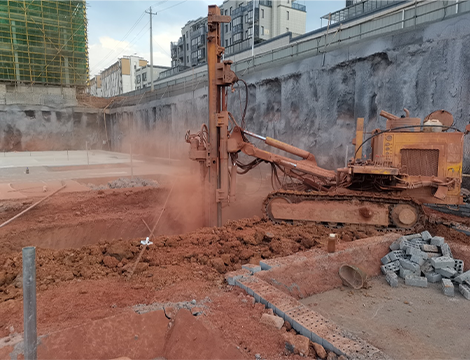
Reliability
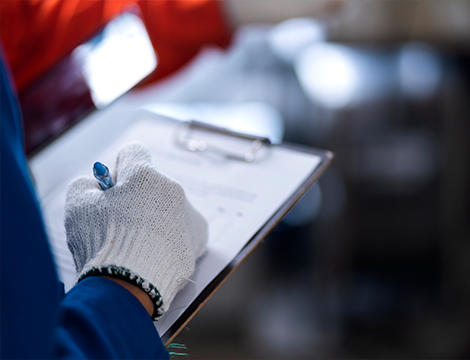
Our DTH hammers undergo rigorous testing and quality control to ensure stable operation even in extreme conditions. Manufactured with high-strength materials and precision engineering, they offer exceptional wear resistance and durability, maintaining outstanding performance even during prolonged continuous operation.
Compatibility
Our DTH hammers are available in various models and are compatible with multiple drilling rigs and systems. No matter what type of drill rig you use, we provide matching DTH hammers to maximize equipment performance. Additionally, our hammers support different drilling media, including dry, wet, and air-water mixed drilling, ensuring adaptability to various geological conditions.
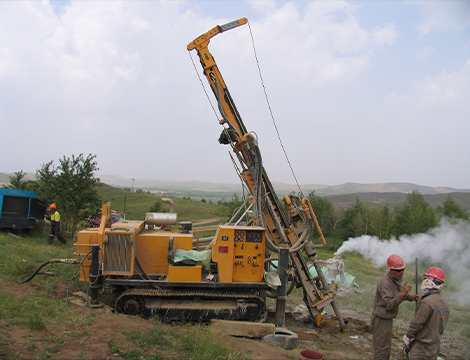
How to Choose the Right DTH
Hammer for Optimal Performance
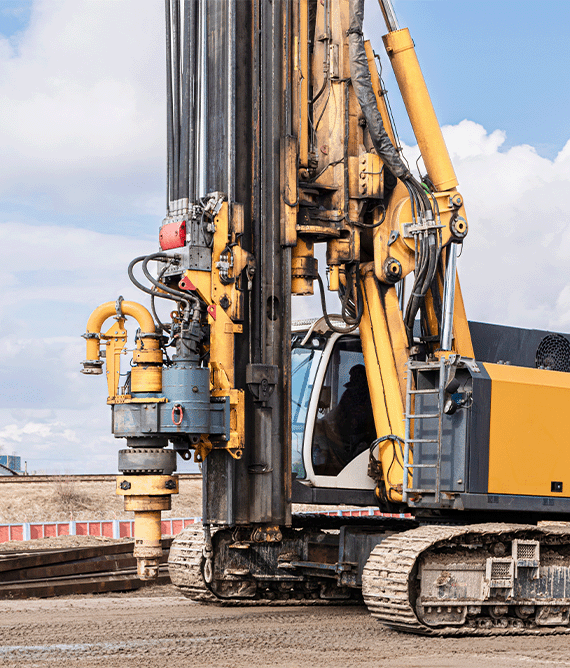
DTH Hammer Drilling Diameter Range
The ideal hole diameter range for DTH hammer drilling is typically between 90 mm (3.5 inches) and 254 mm (10 inches). This range ensures effective drilling efficiency and efficient rock-cutting removal.
· Small Diameter
These holes are typically drilled using top hammer drill jumbos, which apply percussive force at the drill string’s top. Top hammer drill jumbos are suited for medium to hard rock formations.
· Large Diameter
Larger boreholes, particularly those exceeding 10 inches, are usually drilled with rotary rigs, which rely on rotational force and cutting action.
For example, a standard 102 mm (4-inch) DTH hammer can drill a minimum hole diameter of 102 mm (4 inches), while its maximum recommended bore diameter typically falls between 127 mm and 130 mm (5 inches).
Understanding Operational Requirements
To choose the best DTH hammer, consider:
· Rock Type
Select a DTH hammer based on the hardness, strength, and abrasiveness of the rock. Harder rock formations require higher impact energy and more wear-resistant hammers.
· Hole Size
The hammer size should match the required borehole diameter. There should be adequate annular space between the hammer and borehole walls for efficient cutting removal.
· Equipment Compatibility
Ensure the hammer is compatible with your existing drilling rig. It includes connection type, air pressure requirements, and rotational speed.
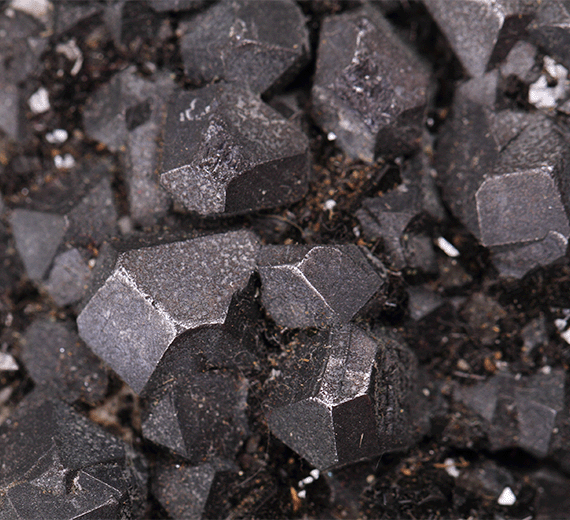
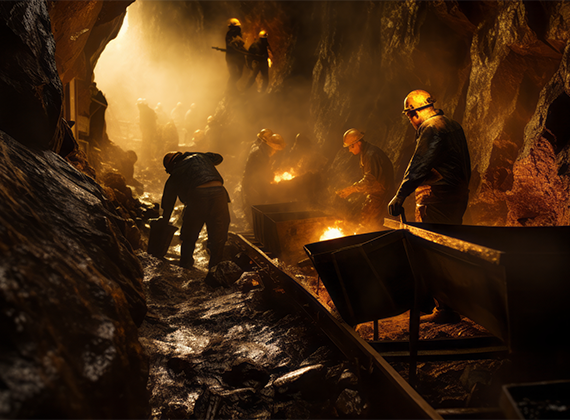
Considering the Work Environment
· Site Conditions
Consider air pressure supply, borehole depth, and whether the operation requires wet or dry drilling. These factors influence hammer selection and performance.
Evaluating Hammer Performance
· Impact Energy
Higher impact energy improves drilling efficiency and expands the hammer’s adaptability to different formations.
· Frequency & Rotation Speed
Proper impact frequency and rotation speed improve penetration rates and minimize equipment wear.
· Durability
Choose hammers made from high-strength materials with wear-resistant designs to extend service life and reduce replacement costs.
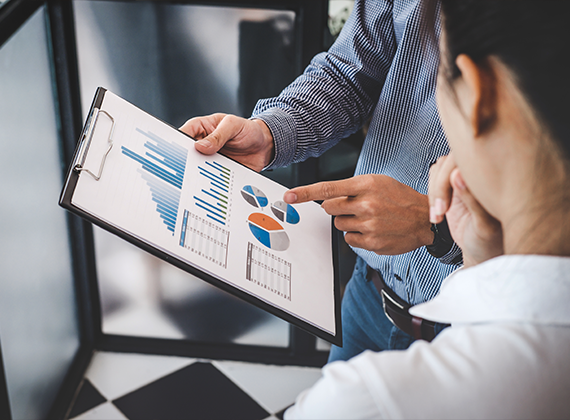
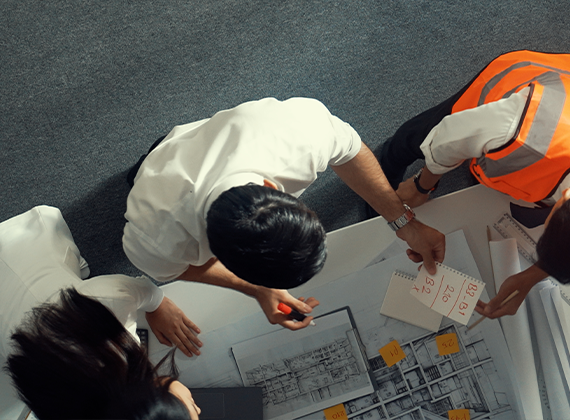
Seeking Expert Advice
· Consulting Manufacturers or Industry Experts
Reach out for technical support and tailored recommendations.
· Reviewing User Feedback
Learn from industry professionals’ experiences to make informed decisions about performance and applicability.